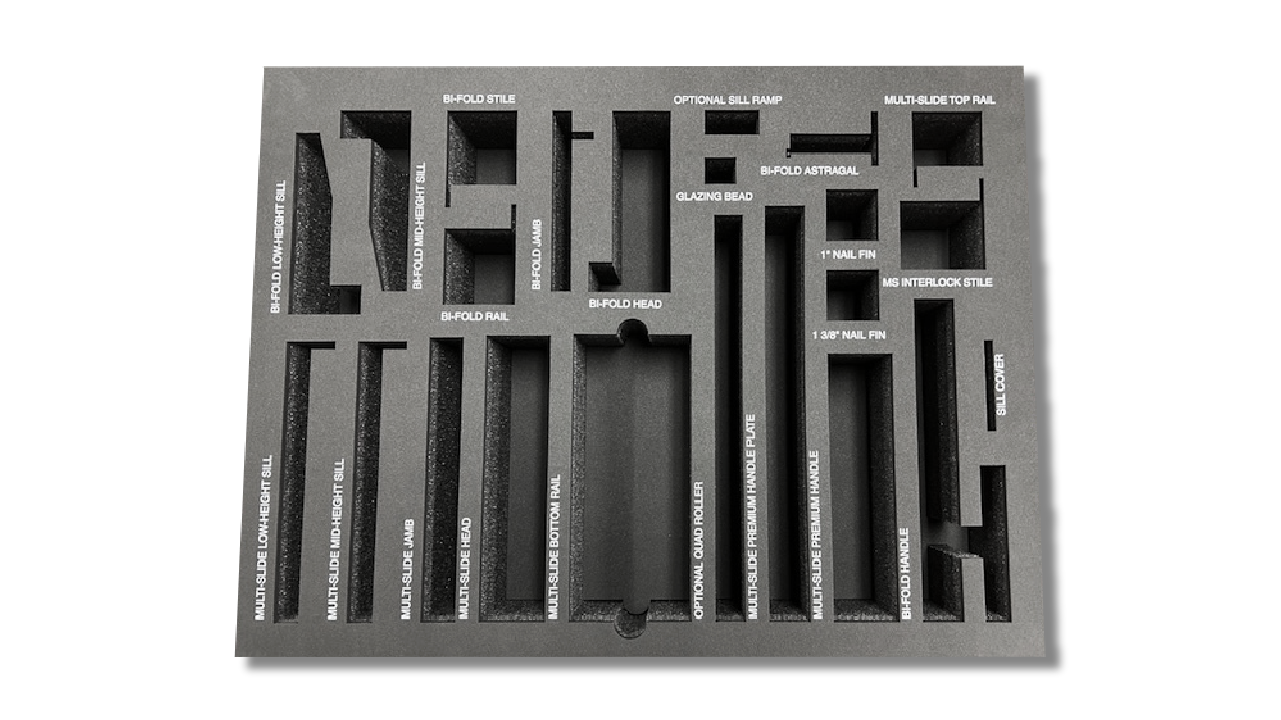
Foam Insert Optimizes Inventory
Our client faced a unique challenge in their product transportation process. They relied on reusable containers to shuttle products between job sites, but a crucial issue persisted. Identifying and managing the products within these containers for assembly and reassembly was proving to be a time-consuming task, leading to inefficiencies and occasional product losses. To address this challenge, our client sought a solution that would streamline their processes and enhance product visibility.
THE PROBLEM
The challenge was clear: our client needed a way to easily identify the interior foam cavities within their reusable containers. They aimed to simplify the task of identifying products for assembly and reassembly on job sites while also preventing product losses when returning to their facility. The existing system lacked a visual cue to indicate which cavities were empty or occupied, leading to delays and potential inventory discrepancies.
THE VIKING SOLUTION
To address this challenge, Viking collaborated closely with our client to develop a customized solution. We recognized that digitally printed foam could provide the visual cues required for efficient product identification. This technology allowed us to create precise and clear labels directly on the foam cavities, making it easy to identify and match components during assembly and reassembly. Additionally, the digitally printed labels also served as indicators, clearly highlighting which cavities were empty when products were returned to the facility.
This innovative solution not only simplified the identification process but also significantly reduced the risk of product losses and streamlined inventory management.
THE RESULT
The implementation of digitally printed foam cavities within the reusable containers brought about several positive outcomes for our client.
- Enhanced Efficiency: The clear and precise labels on the foam cavities simplified the identification of products for assembly and reassembly on job sites. This improvement led to increased efficiency, reduced assembly times, and enhanced overall productivity.
- Inventory Control: The labeled cavities also played a vital role in inventory management. They provided a visual indicator of empty spaces, reducing the chances of products going missing or being misplaced during transportation, which was crucial for our client's operations.
- Cost Savings: By preventing product losses and minimizing assembly and reassembly times, our client realized significant cost savings and improved their bottom line.
Overall, this collaboration between Viking and our client resulted in a tailored solution that not only addressed their unique challenge but also improved operational efficiency and inventory control. It showcased Viking's commitment to delivering innovative packaging solutions that meet and exceed our client's expectations, ultimately helping them achieve their goals in a demanding industry.