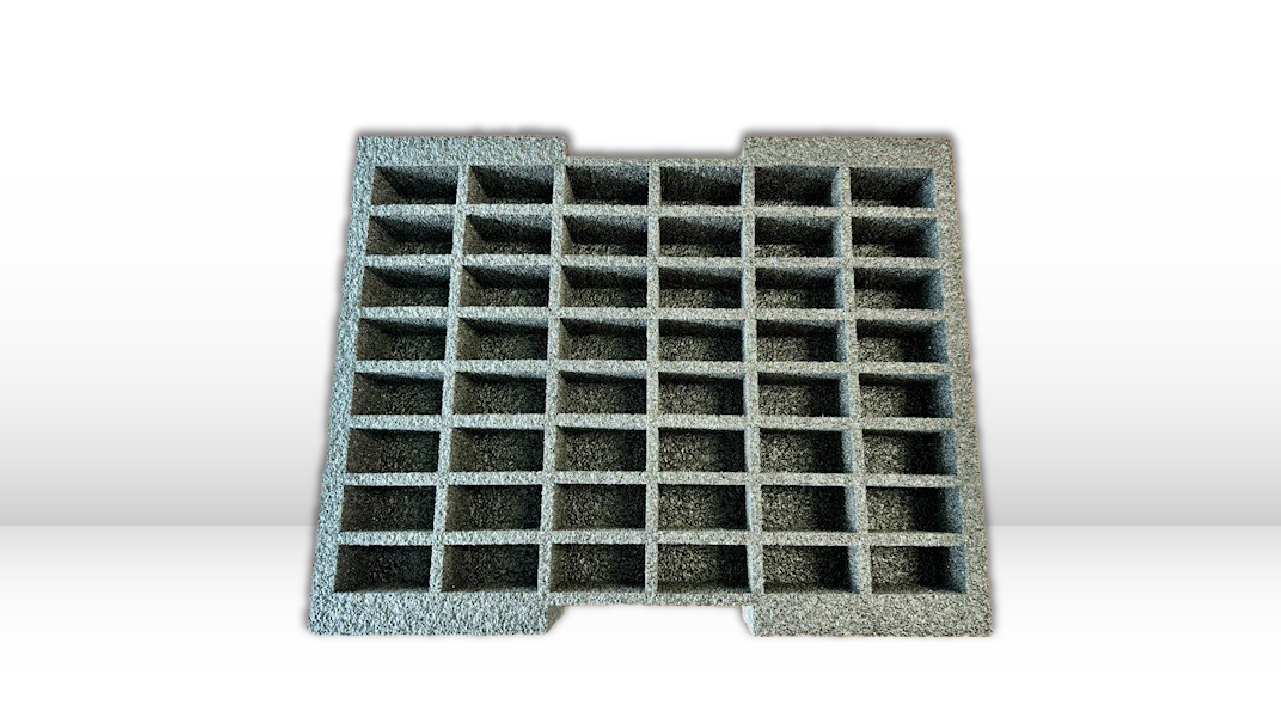
A Cutting-Edge Foam Solution
A client in the electronics industry approached the Viking family of companies with a significant challenge. The company, facing issues with parts procured from overseas due to long lead times and costly tooling, sought a solution that could streamline its operations while enhancing product quality.
The Challenge
The core issue was twofold: the prohibitive cost of tooling for part fabrication and the extended lead times inherent in overseas manufacturing. These challenges not only inflated the production costs but also hampered the agility of the company in responding to market demands. Moreover, the quality of parts, specifically the trays used in packaging electronic components, was compromised, affecting the overall product presentation and safety. The electronics manufacturer needed a solution that could address these challenges head-on, ensuring cost-efficiency, shorter lead times, and superior quality.
The Solution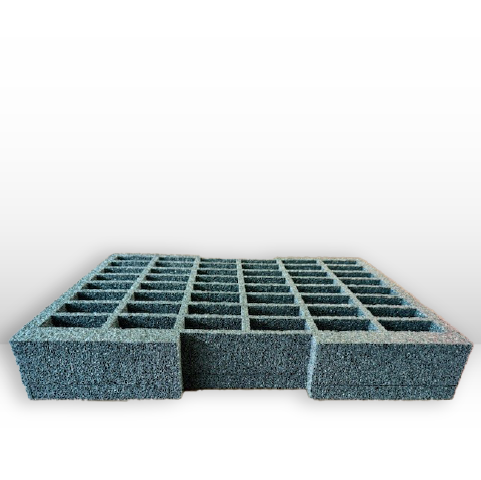
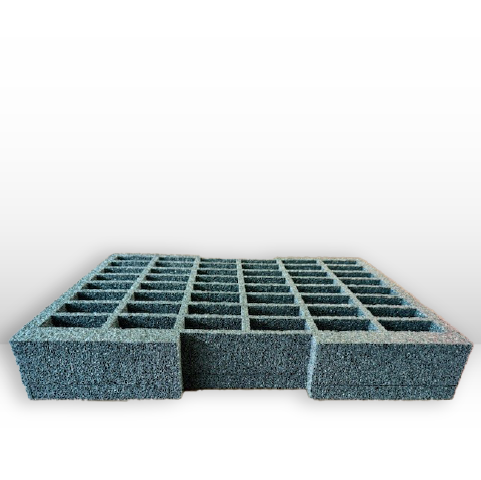
In response to this complex problem, we proposed an innovative solution: the implementation of water jet cut trays. This cutting-edge technology, utilizing a high-pressure jet of water mixed with an abrasive substance, offered a versatile and efficient method for cutting a wide range of materials without the need for expensive tooling. Water jet cutting, known for its precision and ability to cut through materials sensitive to high temperatures like plastic and aluminum, presented a perfect solution to the electronics manufacturer's dilemma.
The key advantages of this solution were:
- Elimination of Tooling Costs: Traditional methods of cutting and shaping parts often involve significant tooling expenses. The water jet cutting technology, however, eliminates these costs, providing a cost-effective alternative for producing high-quality parts.
- Superior Quality: Unlike die-cutting, which can compromise the integrity and finish of the parts, water jet cutting ensures cleaner edges and better overall quality of the trays. This method allowed for the production of trays with superior wall quality, enhancing the protection and presentation of electronic components.
The Result
The adoption of water jet cut trays marked a turning point for our client. Not only did it significantly reduce production costs by eliminating the need for expensive tooling, but it also shortened the lead times, enhancing the company's ability to quickly respond to market demands. The superior quality of the trays, with their cleaner cuts and better wall integrity, improved the presentation and safety of the electronic components, positively impacting customer satisfaction.
This successful collaboration between our team and the electronics manufacturer underscores our commitment to innovative, cost-effective packaging solutions that meet the specific needs of our clients. By leveraging cutting-edge technology and creative problem-solving, the Viking family of companies continues to deliver solutions that not only meet but exceed our clients' expectations, helping them achieve their operational and market objectives.